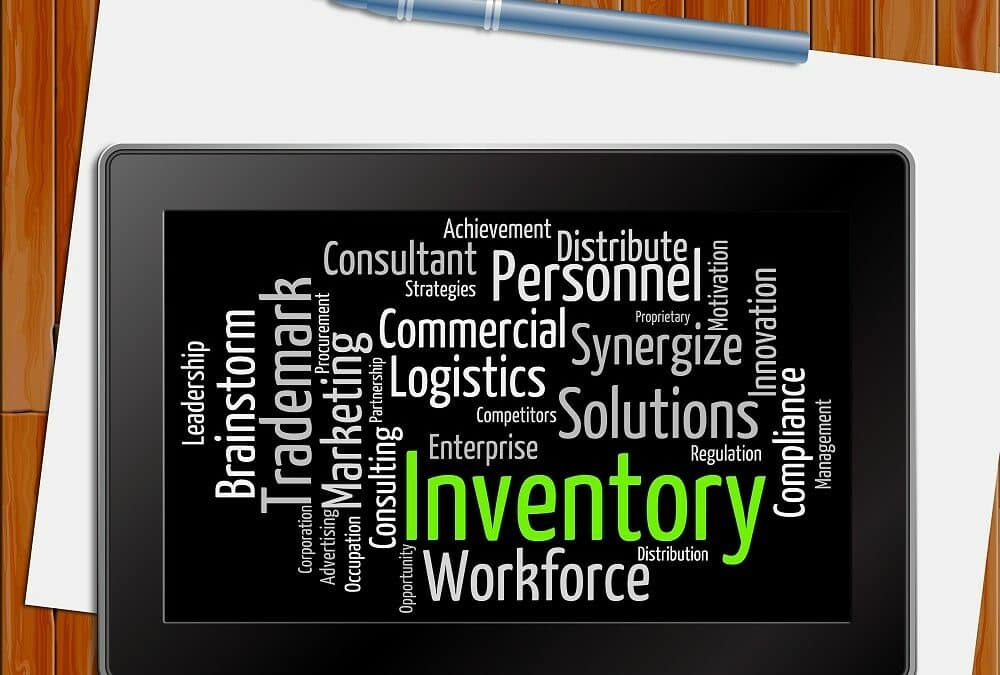
Best Practices in Business Inventory Management System for B2B 📊
Have you ever been in a situation where you’ve had too much stock sitting in your warehouses and running costs just spiralled out of control? Or, the alternative scenario, where you just don’t have enough inventory in stock and can’t supply fast enough to your customers? Today, we’ll learn how to create the best business inventory management system for your company.
>Download Now: Free PDF How to Maximise Margins
If you’re experiencing case no. 1, then you know the pain of watching valuable stock sitting there, gathering dust and eating into your precious cashflows. You know what it’s like to listen to your customers call you a supply risk due to the chaotic approaches of business inventory management in a pricing system.
Obviously, no one wants to be the supplier that takes too long to restock. You’ll lose money and your customers become impatient. What’s worse is you’re risking customer churn.
In short, when businesses can’t buy what they need from suppliers when they want it because it’s out-of-stock or when pricing is way off, they go elsewhere. If this is you, your business not only loses valuable sales that could be worth millions of dollars in revenue, and you get tagged as a risk to their supply.
How can you avoid a supply and demand nightmare?
When you correctly set your inventory’s price correctly, you can accommodate supply and demand dynamics. You also get to create more opportunities to generate healthy cash flows too, without wasting stock.
In this article, we will explain how the best business inventory management practices work hand in hand with the right pricing. We will cover 5 key business stages in inventory management and discuss a system with proven pricing strategies used by B2B suppliers.
These apply to price-overstocked products and deal with supply-side issues. Also, we will share some tips with you on improving your inventory management approaches during peak demand.
At Taylor Wells, we believe that pricing is one of the key levers to make more margin from your stock. Good inventory management enables moving stock efficiently too. This way, you’re not holding stock too long and creating a backlog of costs.
Why is a business inventory management system?
A business inventory management system assists firms in tracking processes from the manufacturer or distributor through storage, and sale. They also have features that provide analysis into your efficiency as well as industry-specific functionality.
An inventory management system, for instance, can be a combination of hardware and software that monitors and handles product inventory, sales, and other manufacturing processes. Having a business inventory management system has advantages. For starters, it reduces human errors, which leads to cost savings and fewer purchases. It also boosts efficiency and productivity by streamlining management processes.
Before settling on an inventory system for your company, learn about your inventory tracking necessities. Smaller firms, such as retail outlets, often employ a basic inventory system, whereas B2B businesses require a system with more arrangements or accounting functions. Larger companies require something more sophisticated, such as an enterprise resource planning (ERP) system.
What are the best approaches/techniques of inventory management?
1. Push Approach
The push technique is a means of moving things from the manufacturers to shops, warehouses, or enterprises. A consumer or employee will then acquire or use the product from the available inventory. To successfully implement this strategy, a company must accurately estimate product demand. Knowing how much of a product is demanded and when is critical.
2. Pull Approach
A retailer, warehouse, or business uses the pull approach when a consumer or employee requests an item. Instead of travelling down the supply chain, an item climbs up. This technique is typically used for speciality items, particularly luxury, or those with little or irregular demand. However, the pull method is not for every firm, especially if clients can get an identical product from some other source right away.
3. Just-in-Time (JIT) Approach
The just-in-time approach is comparable to the pull approach in that an organisation orders inventory just in time to meet a customer’s order or a company’s necessity. Executing this strategy involves dependable suppliers, distributors, and third-party logistics. Without them, a company may fail to fulfil client demands.
How Business Inventory Management System Works For Your Business
Inventory management is part of a business’s supply chain management. It ensures that the business has the right products in the right volume (for sale), and at the right time. When will a specific line of products run out? When should you restock? What are the costs of those items that aren’t selling well?
Basically, you need to have a good understanding of managing your inventory. It involves tracking every item of stock that you have. That refers to products, components/ingredients, goods in stock, production, and sales.
But, a good business inventory management system goes beyond just this. For instance, you thoroughly need to check the difference between dependent and independent demand, or forecast demand to plan ahead. This is especially useful if you want to grow your business in different regions.
1. Opt for a cloud-based inventory management system
Did you know that spreadsheets contain errors? They’re also outdated and slow to update real-time information. Aside from that, it doesn’t sync nor integrate with other analytics tools or data management systems.
It doesn’t have the features of the latest inventory management software that allow you to add or track products and sales channels. So, monitoring sales will often involve manual data entry and calculations which can take much of your time and are prone to human errors.
Cloud-based inventory management systems also prompt you when stocks are low. It also increases productivity with shareable features that can be conveniently sent to cross-functioning teams in your department.
2. Tracking your inventory helps make important decisions for the profitability of the business
With a touch of a button, you can easily access details and receive notifications for sales data and analytics through your sales platforms, the best-selling and least-selling items, compare supplier costs, and automate re-ordering in-demand stocks on the go.
A modern inventory management system saves you time and ensures data accuracy, free from manual error entries. It lets you focus on other aspects like marketing, product development, and growing the business.
Using mobile technology cuts costs on overstock and helps you keep track of major business processes from home and elsewhere. For instance, barcode scanning makes tracking and providing receipts faster. It automates recordkeeping smoothly and eliminates the need to triple-check your data.
Types Of Business Inventory Management System
1. Periodic Inventory Management System
Rather than tracking inventory every day, a periodic inventory system charts inventory at the end of an accounting period, which can be weekly, monthly, quarterly, or yearly. Furthermore, the system does can be operated by hand and manual recording in journal entries. Periodic inventory systems are typically used by businesses that sell few items. A local car accessory store, for example, would use the periodic system because stock levels are simple to record and track.
2. Perpetual Inventory Management System
Inventory is constantly tracked by perpetual inventory management systems. As a result, inventory levels are automatically updated. Purchases and returns are documented in inventory accounts immediately. Bigger companies and those with a large number of inventory units are more likely to use this type of business inventory management system.
3. Barcode Inventory Management System
Barcode business inventory management systems utilise numbers to distinguish each product sold. The barcode numbers can depict a variety of details about the product, such as the manufacturer and supplier the product’s placement, mass, the quantity of each item in stock, etc. This type of business inventory system can benefit companies with high inventory levels. It can assist in avoiding manual system errors and collect the most precise and up-to-date inventory statistics.
4. RFID Management System
Radiofrequency identification (RFID) business inventory management systems go beyond barcode systems. They can read labels from several feet away and do not necessitate scanning in line of sight. Enterprises large warehouses or distribution centres with multi-level stockpiling may benefit from this type of system.
What are the approaches and components of a business inventory management system?
When value components of inventory management and pricing system are weak, a company loses out on profitable revenue growth. They end up with a stock that not a lot of people need. When this happens, the running costs of the business spiral out of control and you may be tagged as a supply risk.
To avoid this nightmare scenario, below are some listed tips for your inventory management guide:
Concentrate on the needs of the business. Managing a warehouse full of inventory can be an intimidating task. So, determine which items are most important and concentrate on these first. Then, keep the top-selling products in stock. It’s a great start to keeping your customers happy.
〉〉〉 Get Your FREE Pricing Audit 〉〉〉
Stocks can either belong to a periodic inventory which needs “periodic” monitoring every 3 to 6 months. While perpetual inventory needs daily or frequent monitoring which includes marking items as produced, received, damaged, replaced, sold, and returned. Both undergo quality checks and stock level accuracy.
Manage supplier relationships. This is significant especially for stock-based businesses. This way, you’ll secure a reliable supply, acquire competitive pricing, and gain knowledge on emerging trends that may affect your business.
Inventory management systems help businesses to stay on top of their inventory. As all businesses have their own unique needs, it’s important to choose a system that matches yours. For example, a global stock-based company like Amazon needs a multifaceted solution that accommodates a huge number of orders processed every day.
Check your competitor’s stock levels and pricing. With the use of competitive intelligence software, you can determine your competitor’s stock availabilities. Then, you can set the most competitive prices on your competitor’s out-of-stock items. Apart from this, you can also track what prices they’re selling at and their volumes. Here’s our guide to pricing tools software.
Here are the latest top picks by Fit Small Business and business.org for the best inventory management software. It’s ranked based on different types of software best suited for B2B retail, restaurants, accounting, barcodes and product tracking, specialty shops, and eCommerce.
5 Key Stages of a Business Inventory Management System
It may seem daunting but stock inventory management is much easier to understand and handle when each stage is broken down. Below are five major stages of how your products start from the suppliers, go into the warehouse, and down to the customers.
- Purchasing raw materials to produce goods or products that are for sale with no assembly needed. In this case, it’s important to use a first-in, first-out approach. That means the first items that were bought must be sold first. This is especially applicable to perishable goods such as food, cosmetics, medicine, and flowers.
- Manufacturing or production for companies that are involved in manufacturing. In the case of wholesalers, they can skip this step entirely.
- Storing the raw materials just before they’re produced or manufactured – The finished products shouldn’t be kept for too long. In fact, the FIFO approach applies to non-perishable items so they don’t end up stuck in storage until they’re damaged and eventually become unsellable.
It’s best to store older products in the front and place the recently purchased items at the back. This gives you an effective chronological order of storing your stocks in terms of the time of purchase
- Sales. Once again, it’s best to use the FIFO approach right from the purchase to storage, then selling the items to customers. Which products have a higher value? Which ones are the most expensive? What are the items that occupy the storage the most? Identify the least expensive products. What items are in between? Categorise them into ABCs.
- Reporting, tracking, and recordkeeping the numbers and data for each sale, covering volume growth, revenue, management, stock levels, and profitability.
Apart from managing these key phases, businesses need to price their stock and optimise their go-to-market strategy. A suitable price can help distributors and manufacturers manage supply and demand dynamics.
Approaches and components of a business inventory management system
- Creating an up-to-date business inventory system helps businesses maintain stock levels. There must be a tracking system for products that are selling the most and those that aren’t. This can also help decrease business costs and further increase sales.
- Businesses can get rid of overstock through annual auditing of inventory management and pricing systems. So, be sure to check your competitor’s out-of-stock products through intelligence software.
- With the help of technology and storing your items in chronological order helps minimise overstocking. Consider this for seasonal products and services too. On the flip side, a frequent shortage of inventory or stock risks customer churn (they buy from competitors.)
- How a business takes care of order quantities, safety stock, replenishment cycle times, seasonality, and forecasts, is very important. It’s best to adjust each operation based on your specific business needs and track what works and what doesn’t.
Conclusion for the approaches and components of an inventory management system
Inventory control is part of the supply chain management of a business. It helps ensure that companies minimise slow growth, and increased costs, and bring flexibility and accuracy in terms of product volume. This largely relies on the size of the business, its model, and the types of products or services.
The best approaches to timely inventory management aid the business in meeting its objectives. That includes sales forecasts, calculations, and figures that predict growth and market trends.
Moreover, businesses should consider the value of the closing stock (trading stock at the end of each income year) and the opening stock (at the start of the next income year). There has to be a balance between overstocking and product shortage as both bring customer and profit loss.
For a comprehensive view and marketing research on integrating a high-performing capability team in your company,
Download a complimentary whitepaper on How To Maximise Margins.
Are you a business in need of help to align your pricing strategy, people and operations to deliver an immediate impact on profit?
If so, please call (+61) 2 9000 1115.
You can also email us at team@taylorwells.com.au if you have any further questions.
Make your pricing world class!
Related Posts
Leave a Reply Cancel reply
Categories
- marketing strategy (26)
- Organisational Design (14)
- Podcast (114)
- Pricing Capability (87)
- Pricing Career Advice (10)
- Pricing Recruitment (19)
- Pricing Strategy (285)
- Pricing Team Skills (13)
- Pricing Teams & Culture (24)
- Pricing Transformation (47)
- Revenue Model (25)
- Sales Effectiveness (27)
- Talent Management (7)
- Technical Pricing Skills (35)