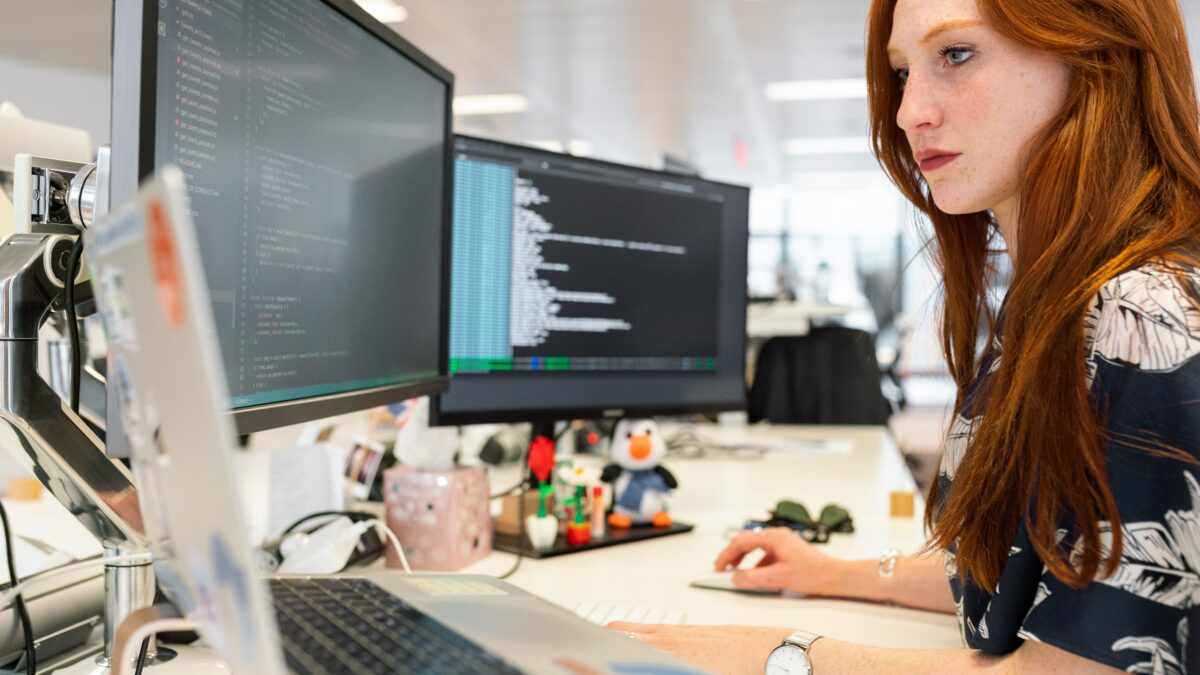
The Most Powerful Business Data Management and Analytics for Every Manufacturer 🏭
Productivity helps boost competitiveness and long-term business profitability. However, the Organisation for Economic Cooperation and Development (OECD) reported that productivity growth in industrial firms has been declining in recent decades. Although there are indications of a comeback, political tensions, such as how different governments respond to economic crises, may continue to hinder progress. Similarly, process manufacturers have struggled as raw material prices have risen and become less accessible. Growth in the industry has indeed become stagnant. Meanwhile, other sectors are modernising using business data management and analytics. So, is it possible for industrial companies to also take advantage of these to hasten their recovery?
>Download Now: Free PDF How to Maximise Margins
Most manufacturers have already implemented conventional adjustments to improve their operations, employing standard methods to extract productivity from their supply networks and facilities. This isn’t enough. Businesses must look for new strategies to boost the efficiency and profitability of their operations. Given their slow growth and unpredictable environment, they must figure out some way to do so much with so little. Fortunately, manufacturers have yet to optimise one of their strong suits which is their business data management and analytics.
In this article, we will discuss three of the most effective business data management and analytics tools and their practical applications. At Taylor Wells, we believe that optimising data from manufacturing processes will increase the company’s overall efficiency, resulting in increased profitability.
We argue that in order to capture the full benefits of analytics technologies, firms must implement organisational changes as they become more data-driven. Then we show how data analytics can improve employees’ life by easing work processes. By the end, you will learn how to use advanced workplace data analytics to achieve major productivity and profitability breakthroughs.
Workplace and Business Data Management and Analytics to Help Improve Production and Increase Profits
Business data management is the process of collecting, organising, retrieving, and safeguarding data from software and services. Using data management helps in effective access to data analytics, which provides the knowledge required to optimise corporate activities and discover chances for change. It entails diverse tasks and processes teaming up to transfer, organise, and encrypt data for it to be exact, clear, transparent, and safe.
Process industries generate massive amounts of data, yet many fail to capitalise on this stockpile of valuable knowledge. Nonetheless, with the latest advancements, such as cheaper computational power and rapidly developing analytics capabilities, manufacturers can now put that data to use. The following sections will go over how.
3 Business Big Data Management and Analytics Skills with Promising Applications
Advanced analytics enhances operational effectiveness in these three use cases.
Workplace and Big Data Analytics Skills #1: Predictive maintenance technologies minimise delays in a fast-paced industry.
To derive insights, predictive maintenance systems collect various historical data, including structured and unstructured, as well as machine- and non-machine-based. Because of this capability, manufacturers can now extend the productivity of valuable assets by using data to predict their failures.
In fact, predictive maintenance decreases equipment failure by 30-50% and extends machine life by 20-40%. How? Companies, for instance, can identify the conditions that are likely to cause a device to fail and check input parameters allowing them to act before failure occurs.
One oil company had issues with its compressors. When one of them failed, the facility had to halt production, costing the business $1-2 million per day. As a result, they devised an algorithm that can forecast the failure of a compressor many weeks in advance.
They found out that high pressure and high temperature, as well as several other variables, were associated with the malfunctions. Even if they can’t completely avoid compressor failure, the company reduced downtime from 14 days to 6 days by pre-positioning workers and repairing equipment. Thus, sparing millions of dollars for each incident.
Big Data Analytics Skills #2: Yield-energy-throughput (YET) helps manufacturers achieve more with less input.
Even a minor increase in operational efficiency can have a big impact on earnings before interest and tax (EBIT). Specifically, YET analysis can boost asset productivity by balancing yield, throughput, and input costs to maximise the profitability of each process stage. For instance, a multinational chemical corporation’s monomers furnace had a highly fluctuating production rate and notably low output. They used business data management and analytics to solve this problem.
Advanced data analysis uncovered key throughput drivers, allowing the development of a process model. It quantified the interrelations of crucial variables and gave a better understanding of the process. The model’s findings were supported by a test run of the furnace. The company then launched tests to improve production. As a result, output increased by 18 -30%, leading to a net contribution gain.
Critical success factors in the Workplace for Big Data Analytics #3: Profit-per-hour (PPH) maximisation streamlines complex production systems.
Predictive maintenance and YET analyses are aimed to enhance the productivity and profitability of individual assets or processes, while PPH maximisation can optimise the cooperation of such equipment and processes.
Let’s take a look at the case of another major chemicals company that sold a diverse range of items to the international market. Its management believed that inefficient manufacturing and distribution decisions were costing the company a lot of money. So, they deployed advanced analytics to put their idea to the test.
They were proven correct as a programming model with over 500 variables probed non-linear cost curves and over 3,000 limitations associated with production, transportation, and agreements. It also found hundreds of production phases with alternative routes and feedback loops, non-linear price curves, raw material cost structures, and inventories.
Through analytics, the company began producing an intermediate product on an unutilised line rather than purchasing it from a third party. They reduced raw material costs by shifting the production of equipment that produced higher yields. Also, they found options to enhance capacity by raising the throughput of several assets. Finally, they increased revenues by increasing production capacity in certain product lines.
As previously noted, using each of the three advanced analytics can yield insights into optimising the efficiency of specific assets as well as the overall manufacturing operation. However, there are additional benefits if you decide to go all-in, employ them all, and become a fully data-driven manufacturer.
The Perks: Workplace and Business Big Data Management Analytics and Skills
When used together, different data analytics enable enterprises to enhance productivity and profitability. For illustration, a major metal factory deployed a mix of digital analytics. The company utilised combined condition monitoring and predictive maintenance with process controls and computerised tracking. Real-time performance visualisation allowed the company to raise production by 50%. While engineers learned more about the failures of equipment and made continuous changes to improve durability. Now, they continue to increase total production by 30% without resulting in higher operational costs.
Continuous data-driven transformation may enable organisations to effectively optimise tactical planning and make better long-term strategic decisions in a complex and evolving manufacturing industry.
Nevertheless, business data management and analytics will not revolutionise process manufacturing alone. Human skills and expertise are still necessary. These new methodologies can only allow manufacturing experts to engage in more evidence-based discussions, assess the impact of various factors on business outcomes, and in many cases, make unexpected decisions to boost efficiency or profitability. So, how exactly can you become a data-driven manufacturer?
Critical Success Factors in the Workplace for Big Data Analytics and Skills
Emerging analytics tools on their own, like any other technology, are insufficient to produce meaningful change. Thus, manufacturers must make adjustments to the people, processes, and technologies to ensure that they can not only collect and analyse their data but also get the greatest value. Here are 5 critical success factors and pointers for data analytics.
1. Be proficient in data management.
Advanced analytics and modelling demand an organised recovery and cleanup of data. This usually consumes up to half of a data scientist’s time. And of course, data analytics requires IT expertise. You will need people to collate data from sensors, including their location, type, and accuracy. Then store the information across several platforms. In this case, you would want a specialised team.
2. Combine analytical abilities with domain knowledge.
Employing advanced analytics in manufacturing necessitates a team from both ends. This includes data scientists, advanced analytics platform specialists, manufacturing experts in areas such as process technology, asset maintenance, and supply chain management, as well as liaisons between such constituencies.
If your organisation doesn’t have a pricing team yet, now is the time to employ one. Our findings show that with the proper setup and pricing team in place, significant gains can happen in as little as 12 weeks. Using smarter price management techniques, the team can capture at least 1.0-2.25% more margin after 6 months. After 9-12 months, organisations are frequently generating 3-7% higher margins annually as they find more complex and previously untapped potentials, efficiencies, and risks.
This combination of expertise fosters efficiency and will most likely produce optimal results.
3. Execute the analytics transformation.
An analytics transformation begins by identifying appropriate processes, challenges and opportunities that advanced analytics can handle. This may include making sense of idle company data and reducing the chances of inaccurate projections. Doing this will show how analytics can be utilised and produce outcomes swiftly.
Some businesses establish analytics laboratories, where teams of professionals may integrate their analytical expertise and practical skills. As the company scales its analytics initiative, the lab may serve as a springboard for new programs as well as a source of knowledge and training. The project can be self-funded, given that high-value use cases are prioritised.
4. Create new business systems.
Business data management and analytics transformation will urge you to reconsider your operational models. In the case of manufacturing, the key to maximising analytics information is to change existing processes. Take, for example, the train sector. A company employed advanced analytics to forecast the malfunction of its engines’ battery packs. Even so, such error warning was inefficient until the corporation modified its maintenance processes.
To make it work, the organisation had to revamp the whole process, including technician deployment, and its spare-parts supply chain. Remember that advanced analytics can only reach their potential when new solutions are merged into day-to-day operations and working procedures.
5. Consider an organisational change.
Manufacturers must consider human factors for analytics to have a strong influence. Accordingly, it is vital to assist staff in becoming familiar with data analytics. Everyone must appreciate how these tools can help them. For instance, they must recognise how analytics will change their roles and possibly improve their lives.
Trust in analytics transformation is needed, otherwise, manufacturers will only see the tools as a burden rather than an advantage, and they will not be able to turn data into insight for actual business benefit.
〉〉〉 Get Your FREE Pricing Audit 〉〉〉
Bottomline on critical success factors in the workplace for big data analytics and skills
Predictive maintenance examines equipment performance data to predict when a machine is likely to break. It reduces downtime by uncovering the causes of the problem. YET analytics, meanwhile, can ensure that machines are as effective as possible, helping to increase yields and throughput while saving energy. PPH maximisation analytics, on the other hand, explores the thousands of factors that influence the entire profitability of a supply chain, from raw material procurement to final sales, offering insight on how to effectively capitalise on given circumstances.
Implementing business data management and analytics into manufacturing operations is complex. To obtain the intended results, analytics should be utilised consistently. Thus, manufacturers must learn big data analytics skills and address this as a continuous business transformation that requires adjustments. This includes shifts in work processes across top leaders, managers, process engineers, and shop-floor operators.
Process manufacturers who can rally their companies to adopt this approach of constantly applying and acquiring advanced big data analytics skills will get the true benefit of these technologies and reach great productivity and profitability milestones.
For a comprehensive view on maximising growth in your company,
Download a complimentary whitepaper on How To Drive Pricing Strategy To Maximise EBIT Growth.
Are you a business in need of help to align your pricing strategy, people and operations to deliver an immediate impact on profit?
If so, please call (+61) 2 9000 1115.
You can also email us at team@taylorwells.com.au if you have any further questions.
Make your pricing world class!
Related Posts
Leave a Reply Cancel reply
Categories
- marketing strategy (26)
- Organisational Design (14)
- Podcast (114)
- Pricing Capability (87)
- Pricing Career Advice (10)
- Pricing Recruitment (19)
- Pricing Strategy (287)
- Pricing Team Skills (13)
- Pricing Teams & Culture (24)
- Pricing Transformation (47)
- Revenue Model (25)
- Sales Effectiveness (27)
- Talent Management (7)
- Technical Pricing Skills (35)