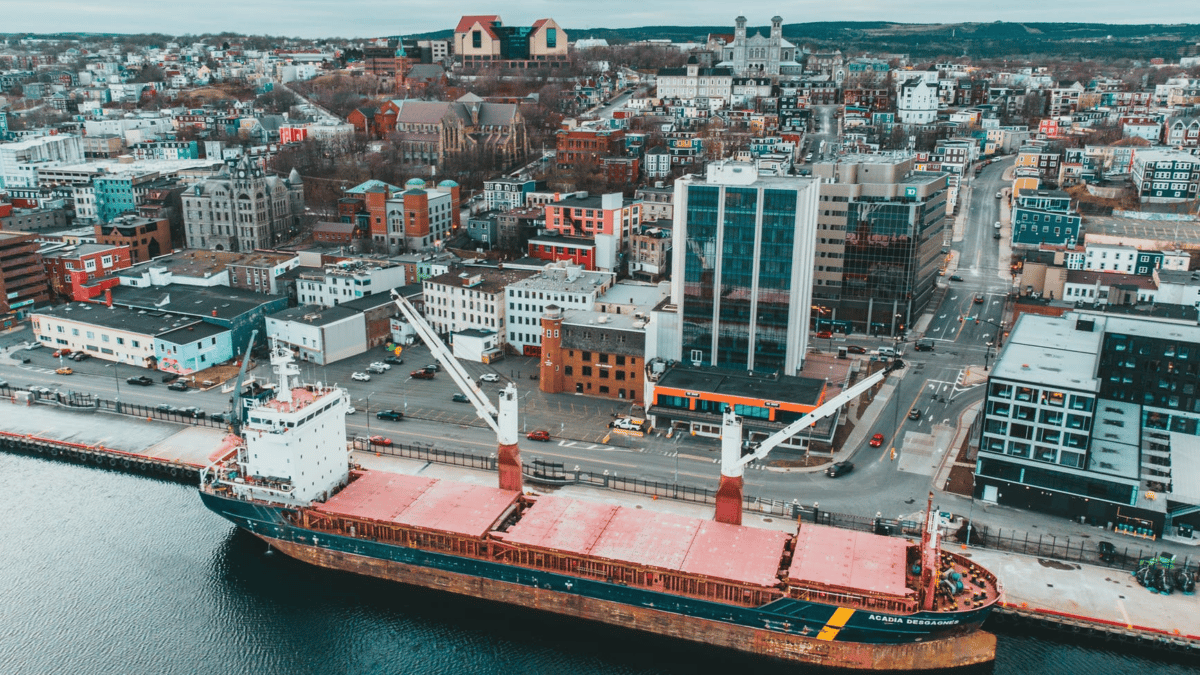
Why Sustainable Supply Chain Strategy Is A Challenge In The Manufacturing Industry 🏭
Covid-19 variants have caused supply chain disruption, bottlenecks, and general chaos across the world in major industries. Some companies are looking for a sustainable supply chain strategy as shipping industries have doubled their waiting lines to the point that delays are expected to last until next year.
>Download Now: Free PDF Organisation Design
Not only has this been a rude awakening during the Christmas season with regard to the duopoly structure of supermarkets in ANZ. But it also put a spotlight on our need to vary up centralised distribution centres, the lack of automated transportation logistics, and inventory management.
Ever since the outburst of the pandemic, we have seen supply and demand equilibrium go out of control all over the world. The horrors of people clamouring to empty supermarket shelves for toilet paper, alcohol, and groceries will remain one of the awkward highlights of 2020.
So, how can a country cope with a sudden and unexpected crisis like the Covid-19 pandemic? What are the challenges that hold supply chains back? And what entails the so-called international alliances? Is it really every nation for itself?
In this article, we’ll discuss the US manufacturing industry and draw out key aspects and learning that are critical for Australian manufacturing. Should factories and manufacturers centralise all of their processes and materials? Or should they offshore and outsource other tasks?
We also ask what are the ways that Australian manufacturers can speed up production to prepare for scenarios like the Covid-19 pandemic. We argue that companies that plan ahead while being assisted by local governments, help manage issues with supply chain, transportation logistics, and inventory management.
What is a sustainable supply chain strategy? Why is it important?
A sustainable supply chain strategy is a deliberate plan of action that businesses adopt to minimise negative environmental, social, and economic impacts across their entire supply chain. It’s about making ethical and responsible choices at every step, from sourcing raw materials to delivering products to customers. Such a strategy focuses on reducing waste, energy consumption, and carbon emissions while promoting fair labour practices and long-term profitability.
Why is this strategy important? Firstly, it enhances a company’s reputation and brand value. Consumers today are more conscientious, preferring to support businesses that prioritise sustainability. Secondly, it can lead to significant cost savings. Companies that optimise their supply chains to be more sustainable often find efficiencies that reduce expenses. Lastly, it future-proofs the business by aligning it with evolving regulations and consumer expectations, reducing risks associated with non-compliance or reputational damage. In short, a sustainable supply chain strategy isn’t just about being responsible; it’s about good business.
What are the key components of a sustainable supply chain strategy?
A sustainable supply chain strategy comprises several key components critical for its success. Firstly, it starts with sourcing responsibly and selecting suppliers who adhere to ethical and sustainable practices. For example, Unilever has committed to sourcing all its agricultural raw materials sustainably, ensuring their palm oil, soy, and tea come from verified sustainable sources.
Next, sustainable strategies emphasise production efficiency, optimising manufacturing processes to reduce waste and resource consumption. An excellent example is Toyota‘s lean manufacturing system, which minimises inventory and enhances production efficiency, reducing both costs and environmental impact.
Additionally, transportation and logistics play a vital role. Companies like Amazon have implemented strategies such as optimising delivery routes and using electric delivery vehicles to reduce emissions and improve efficiency.
A key aspect of a sustainable supply chain strategy is distribution and packaging. Businesses are increasingly adopting eco-friendly packaging materials and optimising distribution networks to minimise their carbon footprint. For instance, Nestlé reduced the weight of its plastic packaging, reducing plastic usage and transportation emissions.
Furthermore, collaboration and transparency across the supply chain are essential. Companies should collaborate closely with suppliers, sharing sustainability goals and progress. H&M, a global fashion retailer, publicly discloses its supplier list and their environmental performance, promoting transparency and accountability.
Finally, continuous measurement and improvement are critical. Regularly assessing key performance indicators (KPIs) allows companies to identify areas for enhancement and track their progress toward sustainability goals. In conclusion, a holistic sustainable supply chain strategy encompasses sourcing, production, transportation, distribution, collaboration, and continuous improvement, creating a resilient and responsible supply chain.
Case Study: A Lack of Sustainable and Customer-centric Supply Chain Strategy in the US Manufacturing Industry
Today, we’ll take on the example of the US manufacturing industry. It has been virally documented how the US like Australia and many other nations’ population were short on masks, PPE (personal protective equipment), over-the-counter medicines, and other basic necessities.
So, why is a first-world country unable to address its abrupt supply and demand issues right away? They’re rather slow in manufacturing products that have a sudden surge in demand during crises.
The US is a major manufacturing source in its global supply network despite the global supply chain crisis for food, medical equipment, personal care items, gadgets and devices like smartphones and computers.
Electronics
Take, for example, product specialisation steps for LED lights, precision devices, cell phones, and hospital equipment. They all need microcircuits and modern tools.
Now, the technology needed in the sudden rise of demand for healthcare equipment is not as simple as we may think. Manufacturers shifted towards subcontractors and specialists who also have to depend on others, eventually.
Some computer brands, for instance, rely on overseas manufacturing in Asia. And their job is to assemble the computer’s original design. But even if they specialise in this area, they still have to rely on other subsystem manufacturers.
The display panel, for example, is made of multiple parts from factories that usually cost billions. And the panel manufacturers can’t finish production without other prerequisite raw materials like circuit connectors, memory and driver chips, glass sheets, hard drives, and so on.
Major Suppliers are Overseas
China, Thailand, and Malaysia are the three overseas specialists in manufacturing. While some computer brands create their own microprocessors, others send them overseas for packaging.
The technological capabilities and skills that are required are now different compared to previous decades. And the upside to this is how the labour workforce is able to use the latest and relevant technologies at a lower cost than ever.
The downside though, is that smaller businesses may face higher costs because some manufacturers may exploit scale economies in the design and production process. This is when the production rate becomes efficient at much lower costs.
On the other hand, well-known electronic brands can’t produce or manufacture without major suppliers overseas which mostly come from Asia – namely Japan, China, and South Korea.
Likewise, pharmaceutical industries in India that need active ingredients depend on suppliers from China. While laboratory industries may source their supply from Denmark. Similarly, Switzerland, Italy, and Germany are the top suppliers of precision equipment and tools.
A Sustainable and Customer-centric Supply Chain Strategy: Interdependency
The Covid-19 pandemic has shown that the interdependency of the supply chain and lack of its management has become obvious. First-tier suppliers are dependent on second-tier suppliers as they rely on a third-tier supplier, and so on.
As automakers like General Motors stepped in to produce ventilators, the U.S. government put the Defense Production Act in place to prevent the public from hoarding supplies. The DPA also limited the country’s export of critical items like medical supplies, PPE, masks, and other basic necessities – increasing the production rate at the same time.
The pandemic has revealed the interdependency of supplier relationships. N95 masks for instance in the US whose manufacturer 3M, shows in its label that it sources its materials globally. But is the reliance on other countries for supplies really the problem? Should brands be reshoring their production?
Analysts say it’s actually the lack of planning from governments in emergency situations such as the pandemic. The “just in time” approach to inventory, logistics, and supply chains has to shift to a “just in case” attitude.
In Australia
On the other hand, Australia’s manufacturing scenario makes up 6% of its GDP, providing 862,000 jobs besides contributing to the country’s exports.
However, the trend of sheltered production is shifting to specialised production. This happens as more buyers demand products and services that are customised to their problems and value drivers. But Australia has yet to realise a more value-added manufacturing process.
An increasing production calls for specialised skills which can help establish a sustainable and customer-centric supply chain strategy
With the clusters of factories in Factory Europe, Factory Asia, and Factory North America, is it really every nation for itself? Or is there truly a fulfilment of international alliances as promised?
Offshoring production such as setting up all the required raw materials, design, and assembly using the right tools calls for specialised skills.
Aside from that, companies have to consider testing procedures with the appropriate equipment. They also need to apply quality control while maintaining talent, resources, and proper handling of materials.
Nowadays, when an emergency happens like a pandemic or other crisis, most US companies are unable to scale up to meet the surge in demand. To make things worse, managing operations has become very much related to procurement transactions.
Setting up a customer-centric supply chain strategy by maximising the use of equipment and factories
Managers should oversee the efficiency of their operational processes and consider it a priority. By using metrics to measure performance, manufacturers mitigate the risks of any surplus activity. They get to monitor and track operations by minimising the costs of surplus.
Another key area to look at is how effective the pieces of equipment are. For instance, Overall Equipment Effectiveness measures the time that a plant or factory is maximising its productivity.
This metric is scored by percentage. So, 100% means that the production rate is maximised. It also means that production materials have no defects.
Most companies though have a score of 85% because it takes time to do maintenance checks, upgrading of new systems or technology, and diversify, if not shift to producing other new materials.
The Role of Capital Investment in Fixing a customer-centric- supply chain strategy
How much capital you’ve put in also matters to shareholders. Some companies subcontract production processes. They choose to outsource other tasks instead.
Then, the contracted suppliers combine demand streams through pooling demand. This distributes the workload and shortens waiting time, allowing them to operate at lower costs.
Most companies prioritise setting up factories that are devoted to their services only. As a result, this constrains the production capacity. It also eliminates the flexibility of manufacturing to meet the sudden surge in demand during a crisis.
Implications
Developing a sustainable supply chain strategy is essential if you want to create a successful, environmentally friendly business model. This strategy should include objectives and goals, as well as the processes and systems that will be put in place to achieve them. It should also include tools for monitoring performance, such as metrics and indicators. Additionally, it should include plans for how the organisation will address any risks or challenges it may encounter.
At its core, a sustainable supply chain strategy should take into consideration all aspects of a company’s operations.
From sourcing to production and delivery, think about each stage in terms of sustainability objectives. Make sure stakeholders are involved throughout this process – their input is invaluable in helping to shape the strategy.
Communication and collaboration are also essential components of a sustainable supply chain strategy. Make sure that all levels of an organisation understand the importance of sustainability, and how it can be incorporated into their daily work. Additionally, engage with partners in the supply chain to ensure that everyone is aligned on sustainability goals and objectives. This will help ensure a successful, sustainable supply chain.
Finally, track progress towards the sustainable supply chain strategy’s goals and objectives to ensure that steps are being taken in the right direction. Measuring progress against targets will provide invaluable insights into where improvements can be made. Furthermore, it helps to create accountability within the organisation and its partners.
By taking a proactive approach to developing and executing a sustainable supply chain strategy, businesses can dramatically reduce their environmental impacts while also improving their bottom line. This is a win-win for companies that are looking to create sustainable operations.
〉〉〉 Get Your FREE Pricing Audit 〉〉〉
Bottom Line
The economic damage of the supply and demand shock that Covid-19 brought may have set off a sense of economic nationalism.
As restrictions revealed vulnerabilities in health industries, international trade wars became increasingly political. More businesses are rethinking the structure of their production and manufacturing capacities.
More countries are ramping up their domestic production rate to reduce interdependency and mitigate complex supply disruptions. And more companies are planning their sustainable supply chain strategy and inventory risk management better as global competition heightens.
In times like these, businesses need to be flexible in finding ways to keep their staff and operations mobilised.
Most business leaders who acted quickly by shifting to automated transactions have coped better than their competitors. They were able to increase tracking activities and visibility on their end-to-end supply chain flow.
To be able to manage better, a company has to cooperate with its partners and clients in finding solutions such as recruiting backup suppliers – or listing down a couple of them, just in case. There should also be a frequent review of incoming and outgoing activities.
Which solutions worked best and why? This enables companies to be more flexible and transparent in their response to what their clients need. Otherwise, those who haven’t invested in relevant technologies to speed up their operations will be left at least 5 years behind, as economists have repeatedly warned quite recently.
For a comprehensive view of building a best-in-class pricing capability in margin-constrained industries, Download a complimentary whitepaper on How to Build Hiring Capability To Get The Best Pricing Team.
Are you a business in need of help to align your pricing strategy, people and operations to deliver an immediate impact on profit?
If so, please call (+61) 2 9000 1115.
You can also email us at team@taylorwells.com.au if you have any further questions.
Make your pricing world-class!
Related Posts
Leave a Reply Cancel reply
Categories
- marketing strategy (26)
- Organisational Design (14)
- Podcast (114)
- Pricing Capability (87)
- Pricing Career Advice (10)
- Pricing Recruitment (19)
- Pricing Strategy (287)
- Pricing Team Skills (13)
- Pricing Teams & Culture (24)
- Pricing Transformation (47)
- Revenue Model (25)
- Sales Effectiveness (27)
- Talent Management (7)
- Technical Pricing Skills (35)